TTR Turret Center Driven Rewinder
Automatic Transfer Rewinder
The main HMI screen is easy to use for the operator and allows full interaction between the machine and the operator. It incorporates diagnostic information for any failure and makes preventive maintenance simple, thus reducing the unforeseen downtime and increasing machine availability.
The TTR is ideal for many applications and processes such as coating, printing and printing. The different rewind options guarantee the possibility of unwinding a wide range of materials.
The latest technology in safety and control has been incorporated into its design, allowing quick and easy integration with other control systems, whether it is a new installation or the improvement of a line existing.
The TTR is available in different sizes and levels of automation as well as different options to ensure the best adaptation to the specific needs of each client.
With the TTR a perfect quality winding is achieved, without lateral movements (thanks to the telescopic reels) and high tension (obtaining reels that avoid problems both during transport and storage). In short, a perfect winding is achieved that guarantees the absence of overlaps and wrinkles during the process. In addition, the reel control prevents possible damage after cutting the paper.
MTorres offers in its TTR model a turret-type rewinder that is characterized by using the "center driven" rewinding technology with the incorporation of a nip system that allows you to precisely control the hardness of the reel throughout the rewinding process.
Its high performance, coverage of the range of sizes of reels and materials to be rewound gives it flexibility and applicability in a multitude of processes. Its robotic core handling system allows it to adapt flexible to different needs and spaces and provides a complete solution to the entire rewinding phase. The TTR model has different size configurations with two width ranges of up to 1400 and 1700 mm and rewinding diameters of up to 2185 mm. It can be used with different sizes of cones and it has a robotic core handling system to facilitate its handling in an ergonomic way. It has a Nip system as well as a braking system from the surface to maintain the integrity of the last turns after the reel change. A large number of Settings are available that will allow you to adapt to the most demanding processes.
Settings
Settings / variants | improvement area | |
---|---|---|
Mandrel handling system | Mandrel handling by robotic system | Process efficiency / ergonomics |
Automatic gluing | mandrel preparation by Hot Melt automatic application system | Process efficiency / ergonomics |
Reel evacuation rails | Reel Handling | Process efficiency / ergonomics |
Automatic reel evacuation door | Reel Handling | Process efficiency / ergonomics |
Turning bars | Band handling for flipping | Process quality |
Aligner | Band management for alignment | Process quality |
Different cone diameters | Spindle handling | Customization |
Rockwell Platform | Rockwell Model of PLC, Drives, Display, communication | Customization |
"Factory Towers" | Operational availability monitoring and improvement tool for productivity improvement | Process efficiency - productivity |
USA Regulations | Marking / regulations | Customization |
MT Rewind Tests | Tests | Machine optimization |
Other non-CE language | Documentation | Customization |
Imperial unit system | Documentation | Customization |
Recommended Refill Pack | Refills | Maintainability |

Reel evacuation rails

Turning Bars

Automatic door

Automatic gluing installation

Automatic gluing

Core Handling
TTR manual mandrel loading
TTR Rewinder
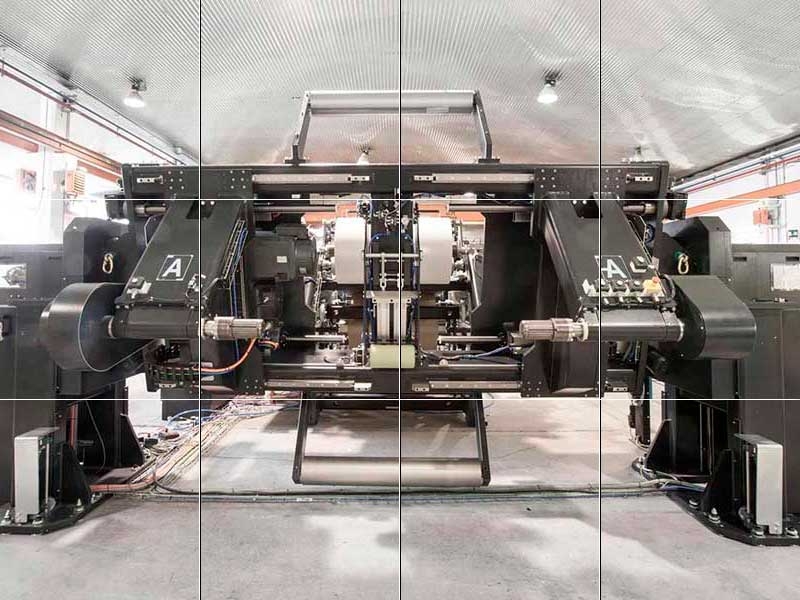