FLEXIBLE DRILLING HEAD
5-axis riveting drill
Competitive solutions for small diameters
The FDH is a 5-axis interpolated drilling machine with a modular design to facilitate system customization.
Its principle is “walk” above the aircraft fuselage and fix its position using a set of vacuum cups. When the FDH drives into position, it locks with the vacuum cups and is ready to perform drilling/riveting operations.
After drilling/riveting a given area, the FDH takes another step as follows: it releases half of the cups and moves them forward, where it will place them again for drilling. next drilling/riveting operation.
The FDH does not need any additional guidance system attached to the aircraft to move around its fuselage, regardless of its position, even upside down.
The FDH is a 5-axis autonomous platform that has the necessary end effectors for drilling and countersinking.
The FDH is configured on site by two operators and in 5 minutes.
Optimal robot design ensures maximum positioning accuracy for drilling and countersinking, as well as high-speed performance with minimum weight.
A vision and laser system ensures that the FDH follows the desired path and the appropriate CNC program from the theoretical path applied to reality.
The FDH can work and run on most current aircraft models, from the smallest to the largest passenger aircraft.
Its applications are drilling and riveting in circumferential, longitudinal and conical joints.
A portable electrical panel is supplied, connected to the FDH through a harness with minimal wiring.
A control system developed by MTORRES allows the FDH to work without the need for a conventional CNC system.
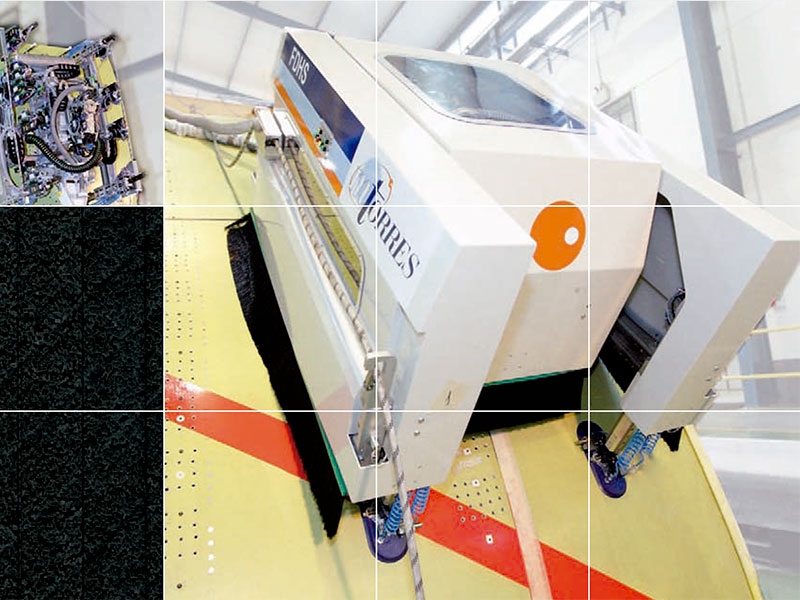
- Number of strips
Normally 12, 16, 24 or 32 - Width of strips
Normally 12, 16, 24 or 32 - Minimum strip length
Normally 12, 16, 24 or 32 - Maximum speed capacity
Normally 12, 16, 24 or 32
Production support
Robot that walks the fuselage to typically drill joints from both the upper half to the lower half as well as two consecutive sections of fuselage.