26-04-2022
MTorres awarded with the JEC Composites Innovation Awards
IIAMS Clean Sky project, in the Aerospace Process category, has been recognized as the most innovative project in its category. This Innovative Infusion Airframe Manufacturing System – IIAMS – simplifies the manufacturing process of composite components and has been developed together with Airbus.
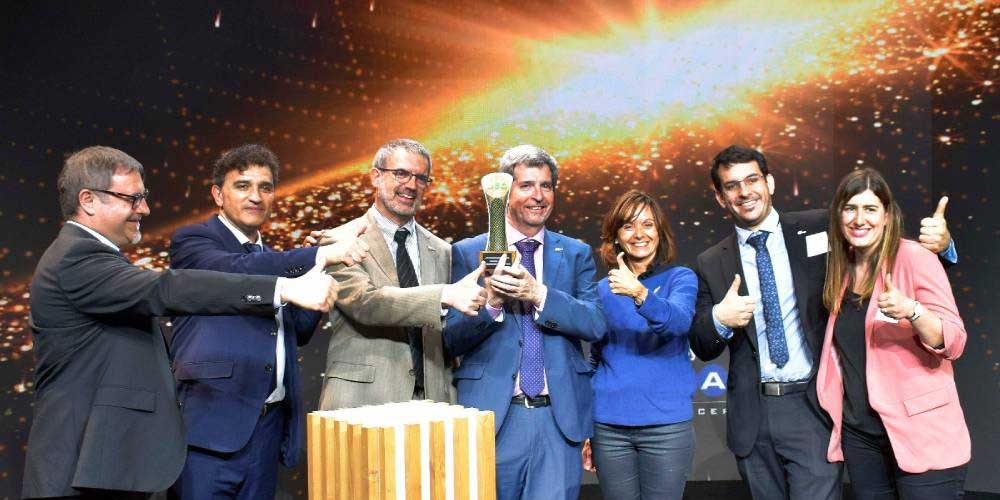
IIAMS project opens a new future for composite materials processes adding several benefits from process simplification and flexibility to cost, energy and weight savings in the final parts, together with the creation of fast implementation and deep optimization of all the stages. IIAMS demonstrates how the manufacturing processes of the future will be shaped.
This innovative approach has been already demonstrated through the manufacturing of the lower side of the wing-box of the Airbus C295 aircraft. In collaboration with Airbus, and under the support of the Cleansky2 Workframe, the complete project has been designed, prototyped, evaluated and tested, with excellent results both in processing and final component performance.
For more than 20 years, JEC Composites Innovation Awards has celebrated successful projects and cooperation between players of the composite industry.
This is the third time MTorres has been distinguished as the company was already awarded in 2018 for the new automated manufacturing process without mold for monocoque fuselages in composite material, Torreswing project, also within the Aerospace Process category. A few years before, in 2011, the new blade technology with a revolutionary,100%-automated manufacturing process, Fibramatic project, was also awarded in the Wind Energy category.
Besides, in this occasion, one more project developed by MTorres was chosen as finalist within the Equipment and Machinery category, our TorresPrint3D® , an innovative additive manufacturing process.
Sebastián Díaz, IIAMS Technical leader, has received the award on behalf of MTorres. He has thanked MTorres team for working so hard and Airbus team who has done everything easy. He also has had some words to dedicate the award to MTorres founder, Mr. Manuel Torres: "He was not only the head, but also the heart of the innovation department. He taught us we can get everything in life, that nothing is impossible and that we have to follow our dreams". "This is for you, Manuel, we are following you, your teaching, we are keeping on innovating".
During the ceremony he has been accompanied by Ms. Yolanda Torres, Executive Vicepresident of MTorres; Juan Albéniz, General Manager of the company; José Manuel González, Chief Technical and Innovation Officer; Iñigo Idareta, Head of Special Projects department; Valentín Forte, TorresPrint3D Project Manager; Coro García, R&D Financing, IP and TSCI Management. The MTorres Delegation was accompanied by two Airbus representatives from the IIAMS project: Francisco Javier Guerrero and Luis Rubio.
INNOVATIVE INFUSION AIRFRAME MANUFACTURING SYSTEM - IIAMS
Can you imagine an aircraft without fasteners? A manufacturing line that can be shipped immediately to a new site? A complete digitization and real time control of the process? This could be the future, but this is what we call IIAMS.
This Innovative Infusion Airframe Manufacturing System is the result of the vast composites know-how at MTorres, the large experience in infusion processes and the bet on innovation that the company has supported since its foundation.
The goal of this proposal is to simplify the manufacturing process of composite components, looking for:
- The elimination of the autoclave
- The reduction or even elimination of fasteners and mechanical joints
- The flexibility of the process layout and its transportation
- The exploitation of Industry 4.0 tools
- The focus on sustainability, reducing weight and manufacturing steps to achieve more efficient results
There is one material solution which is key for the achievement of mentioned results: the use of dry fiber materials. Using liquid resin infusion process the need of an autoclave can be avoided, and through a smart infusion configuration, the multiple initial components can be combined in a single final part, one shot infused, with no need for additional assembly steps after the combined curing.
The project has created a complete, portable production process and associated hardware that generates a final part composed by the skin, the spars with their stiffeners and several skin stringers. The development of the ACTI (Automated Center for Thermo Infusion), with a complete real-time control and advanced sensoring for infusion and curing monitoring has been one of the key milestones achieved in the project.
ADDITIVE MANUFACTURING TORRESPRINT3D®
Additive manufacturing is a technology that allows the production of complex geometries with an unprecedent flexibility in the manufacturing process. Although many solutions can be found in the market, are they good enough for large industrial components production?
This is the focus of the MTorres TorresPrint3D® technology, to find a solution that can benefit from the opportunities that additive manufacturing offers, such as design flexibility, short lead-times, or material waste reduction, in a solid, reliable manufacturing process that can achieve the production of very large components.
The patent pending TorresPrint3D® technology developed introduces several critical innovations, including a compact configuration that avoids the need of a heated chamber, and a horizontal printing nozzle configuration that allows the production of large horizontal components avoiding usual risks.
There is a requirement in additive manufacturing for the heating of the parts to complete a robust, high quality production process. This aspect is commonly solved with the use of heated chambers, a solution that nonetheless implies a limitation on the global size of the final parts. TorresPrint3D® incorporates a reliable and tested heating system directly on the printer head avoiding that need, removing those size limits.
Together with a smart configuration, TorresPrint3D® allows the production of large components, with the part growing over a movable table, where size limits are imposed only by the final production site.
TorresPrint3D® proposes a coupled manufacturing system, where there is an additive manufacturing focused equipment, based on a configurable platform (such as robots, gantries or hybrid) depending on the workspace required, and a specific machining platform, that achieves the expected dimensions tolerance and surface finishing. The options, however, are immense, with the possibility to introduce multipurpose manufacturing systems with automated manufacturing head exchanges, introducing additive manufacturing, machining or even more.
For more information, please contact us:
MTORRES DISEÑOS INDUSTRIALES SAU
Ctra Pamplona Huesca km 9
31119 Torres de Elorz (Navarra) Spain
Tel: + 34 948 317811
www.mtorres.com
info@mtorres.com